Materials
Concrete structures fit for a low-carbon future
Researchers at ETH Zurich in Switzerland have developed a concrete floor system that uses 70% less material compared to traditional reinforced concrete. Susanne Hauner speaks to project leader Professor Dr Philippe Block about plans to bring the innovation to market, and how concrete fits into a greener building future.
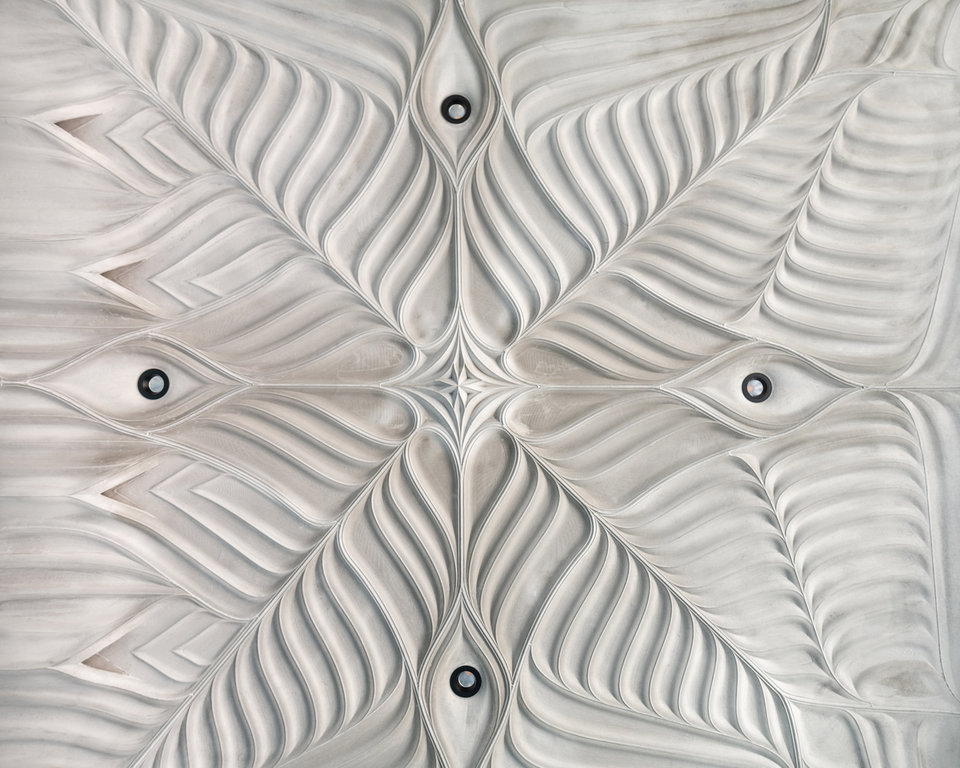
Is
there a role for concrete in a net-zero built environment? As concrete is one of the most widely used building materials around the world, it’s unlikely that we can phase out our dependence on it by 2050. However, work is underway across the design and build industry to find more sustainable solutions to concrete construction.
One such innovation comes out of Switzerland, where researchers have developed a lightweight funicular concrete floor, that could offer an alternative to traditional concrete floor slabs with significantly lower material requirements and associated emissions.
The floor system is being developed by the Block Research Group at ETH Zurich in partnership with building material company Holcim. It has recently seen its first installation in HiLo, a new unit at the NEST experimental building on the campus of research institutions Empa and Eawag in Dübendorf, Switzerland.
We caught up with Dr Philippe Block, Professor of Architecture and Structures at ETH Zürich and the founder of the Block Research Group, to find out more about the floor system and its potential in construction.
Bea Sennewald, director of projects at Article 25
Bea Sennewald, director of projects at Article 25
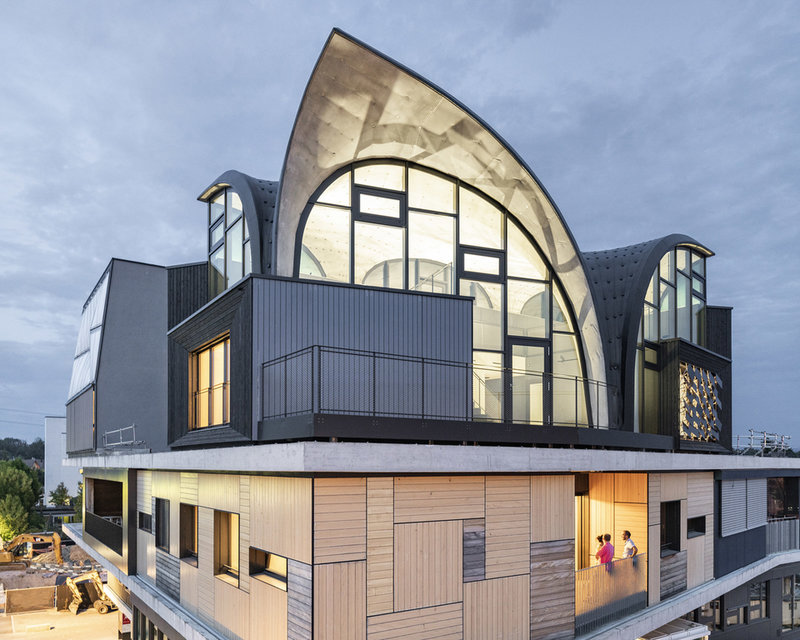
The floor system is one of the innovations demonstrated in HiLo, the newest unit at the NEST building. Photo: Roman Keller
A new floor system inspired by historic structures
The result of more than a decade of R&D, the Rippmann Floor System (RFS) is a rib-stiffened funicular floor system. It applies centuries-old principles of masonry to a cast concrete structure with the aim of using as little material as possible, thereby reducing raw material use and embodied emissions.
Unlike traditional reinforced concrete floor slabs, which use large amounts of concrete and reinforcement steel, the RFS offers a hollow solution using unreinforced concrete. It consists of a thin, doubly curved funicular shell with vertical stiffeners, which transfers loads to the supports through compression only. The resulting forces are accumulated in the corners where they are cancelled by post-tensioned ties.
“By placing material only where it is structurally needed, following the flow of forces in compression and tension, and by keeping all materials separate, the floor system saves more than 70% of concrete and 90% of reinforcement steel compared to the standard reinforced concrete slab,” Block explains.
“Considering that in a medium high rise, 40% of the mass is in the floor slabs, the potential impact and the scale of this innovation becomes abundantly clear.”
Having these vaulted geometries not only allows us to reduce the volume of material, but also to have very low stresses, and that means that we can use weaker materials.
The idea of placing material only where it is structurally needed is inspired by “principles that make gothic cathedral stand for centuries”, such as vaults and arches, Block adds.
“These historic structures and principles that we are reintroducing become relevant today because of our climate crisis and the pressures on it caused by the built environment. Having these vaulted geometries not only allows us to reduce the volume of material, but also to have very low stresses, and that means that we can use weaker materials. Weak materials mean less associated emissions.
“At this point in development, on top of the reduction in volume, we reduced the material emissions of the concrete by 70% and I expect this to only get better in the coming years.”
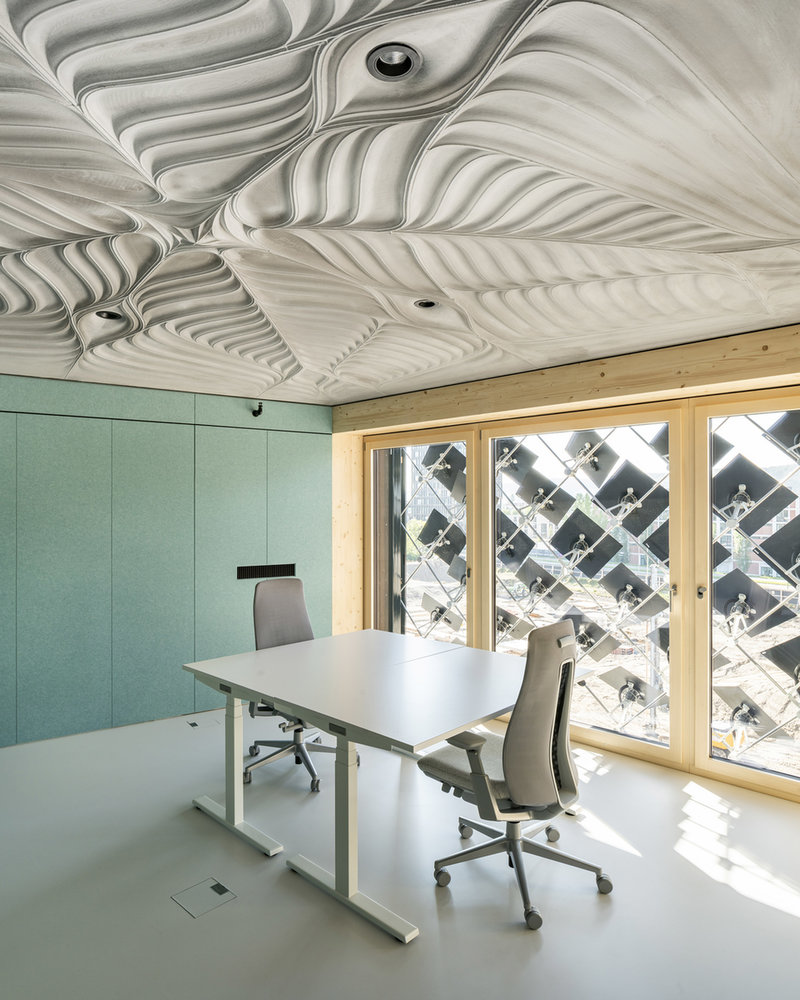
An office in the HiLo building unit with a view of the bottom surface of the lightweight floor construction. Photo: Roman Keller
The road to market
With the first real-life installation successfully completed, the Block Research Group is now working in partnership with Holcim to scale up the RFS and bring it to market by 2023.
The team plans to commercialise the RFS as a prefab solution and optimise it for use with existing manufacturing infrastructure and installation strategies. For example, initially, prefabrication could be carried out using recyclable plastic 3D-printed moulds, which are already available on the market.
Block imagines the path to market could involve a ‘catalogue’ of standardised modules a customer can choose from, but custom designs to optimise the floor system for a specific building could also be an option. The team is also exploring potential partnerships with prefabricators to make the most efficient use of existing production pipelines.
The team plans to commercialise the floor system as a prefab solution and optimise it for use with existing manufacturing infrastructure and installation strategies.
Further R&D work over the next one to two years will inform the business model and answer some of the “very pragmatic questions” that need to be addressed to commercialise the system, Block says.
This includes demonstrating the floor system complies with building regulation standards with regard to acoustic performance, fire safety and thermal mass - all of which can be challenges in lightweight structures due to the reduction in mass.
Block is confident, based on the team’s research and modelling, as well as the experience with and measurements taken at the HiLo demonstrator, that not too many compromises on efficiencies will have to be made for the RFS to meet regulatory requirements in those areas.
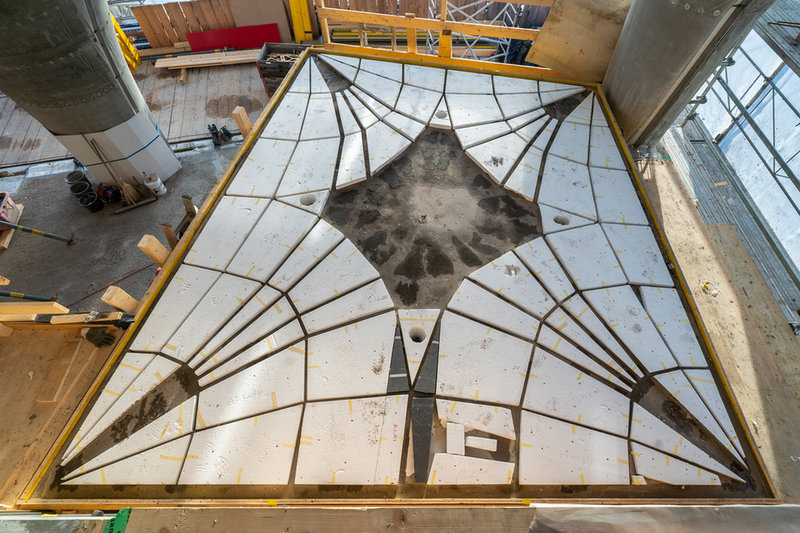
Top view of the rib-stiffened funicular floor system after concreting, during the installation at the HiLo building unit. Photo: ETH Zurich, Block Research Group | Juney Lee
What’s the target market?
Block sees potential applications for the RFS in medium high-rise buildings, as prefabrication speeds up construction and reduces waste. More importantly, he says, the weight saving from the lightweight floors benefits the vertical load-bearing system and leads to further material savings, including in the foundations.
Office buildings are an obvious target due to their modularity, and because building systems, ventilation, plumbing and other systems can be integrated inside the cavities of the RFS. This creates a space saving in between floors, meaning it would be possible to fit more floors into a building without adding height. In a 150-metre tower, for instance, this could add up to “a couple of floors, if not towards half a dozen of floors more”, Block says.
Another target for the system is the residential sector, where the most typical floor solution in medium high rises is the reinforced concrete slab. Here, the team believes its solution could become competitive quickly, as it offers an alternative with significantly reduced material requirements.
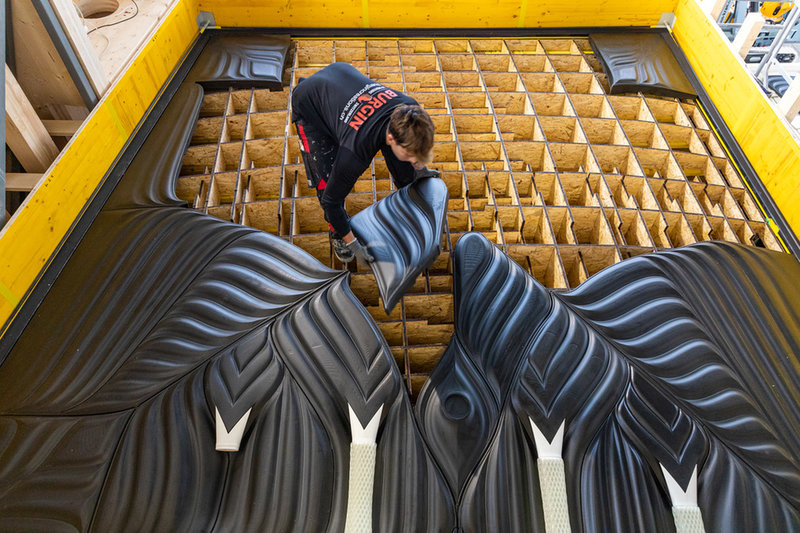
Assembly of the 3D-printed formwork components, designed by the Digital Building Technologies group at ETH Zurich, for one of the rib-stiffened funicular floor in the demonstrator installation. Photo: ETH Zurich, Digital Building Technologies | Georgia Chousou
Scaling up to new heights
Block’s team hopes to take the next step in scaling up with a 150m tower project designed around the floor system. The project details are still confidential, but he expects applications for building permits to be submitted in the coming weeks.
For this project, the team is developing the RFS to be dry assembled and ‘clicked into place’ without the need for scaffolding. Dry assembly also means potential full reversibility at the end of life.
“We use the masonry model so that we dry assemble our prefab system,” Block explains. “We don't need difficult to reverse chemical connections, like glue or mortar, and we don't need mechanical connections, so one could really imagine a proper reuse of all the components that we install. Because we are being very disciplined in separating materials, we have clean end of life and low-energy recyclability opportunities.”
The consultation carried out for the planned tower project assessed the RFS against other available options, including hollow-core solutions. “We came out practically cost-neutral against hollow-cores, but our embodied carbon was only a third,” the team said of the results.
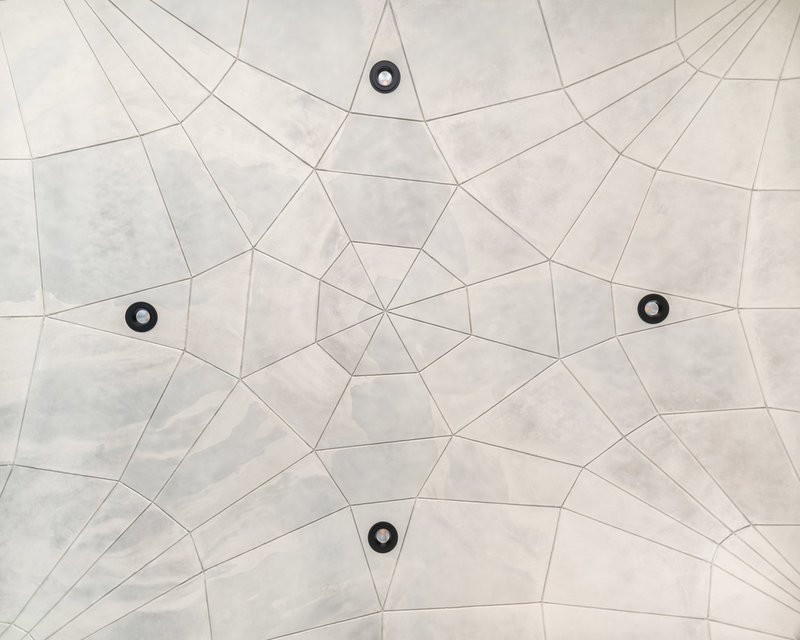
A view of the lightweight floor construction with integrated building systems from below. Photo: Roman Keller
A greener future for concrete?
The world's population is expected to increase by 2.1 billion people by 2050. To provide adequate infrastructure and housing for future generations, it is estimated that 200 billion square metres of floor area need to be built in the next 30-40 years.
Block believes concrete can play an essential role in this, as it is an established and widely available material. Although there has been a lot of “concrete shaming” lately, he says concrete is an “extremely good material” which mainly becomes problematic due to the vast quantities we use.
“If you, for example, look at the embodied carbon coefficient per-unit mass of concrete versus other materials, we're all the way down the bottom,” he says. “Unreinforced concrete also has a very clear end-of-life strategy, so if you don't reuse the components you can easily recycle it. What is important about that is that we are not just focusing on the emissions, but also on the reuse of resources, instead of virgin materials.”
These really significant changes can only happen when we also design with a bit more restraint and discipline.
Block sees great potential for lightweight, resource-saving concrete construction in much of the developing world, which has huge demand for new housing and infrastructure.
“If you apply this to the increasingly common typology we are already seeing in China and India, and that is upcoming for Africa, [which is] the medium high rise, the impact really starts to scale. If you project the numbers of what it means for one of these buildings, and then you imagine the millions of buildings that need to be built, I think it really becomes clear what is possible by innovating on even the most banal element a in a building, that there is real value in structural design.”
How far such innovation can go also depends on architects, though. “These really significant changes can only happen when we also design with a bit more restraint and discipline,” Block says. “We have to start from the constraints that such systems offer. It demands a different approach to architecture than the one that was celebrated until very recently, but I see that everyone is increasingly starting to understand our responsibilities.”
Main image: The demonstrator installation of the lightweight floor construction with integrated building systems, seen from below. The air outlets of the ventilation system are visible at the left of the image. Photo: Roman Keller